This is the video that i have created, It uses photo stills to create a stop motion effect. I source the music from a site called www.newground.com. The filming was done over the course of 4 days and it was edited in 3 days over lapping the filming. This allowed me to capture extra footage if i needed to. Mark was one of the people i spoke to in the FIND stage of the project and felt it would make sese to invite him to be in my video. I also asked a few classmates to fill in for people who were unable to attend the days filming.
Wednesday 12 May 2010
My promotional work
These are some of the website that i have tried to distribute my work on. I have place my work on Open:output, Designspotter and Behance. I also used my research Twitter to spread the word of my product.
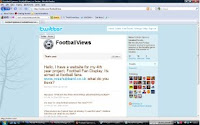
Promoting My work on my FootballViews research twitter.
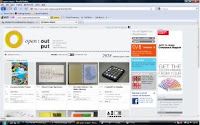
My Profile on Open: Output, ranking at 89/2900+
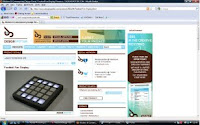
My Work on Designspotter, (3.33/5 stars)
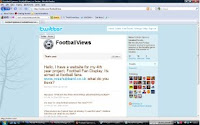
Promoting My work on my FootballViews research twitter.
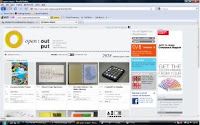
My Profile on Open: Output, ranking at 89/2900+
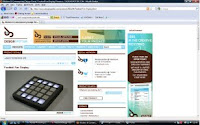
My Work on Designspotter, (3.33/5 stars)
My Website
These are screen shots of the website that i have produced, I used 1and1.com to attain the domain name and my flatmate has said he will host for free. I published the website in the drag and drop software IWeb. It was very very easy to use and the templates are very professional looking. It consists of 6 pages, Home, Press Release, Press Images, Video, My Profile and Contact Page.
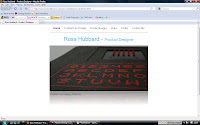
The Home Page
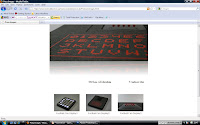
The Press Images Page
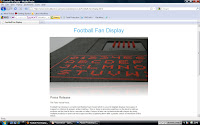
The Press Release Page
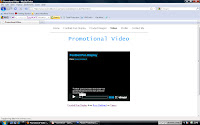
The Video Page
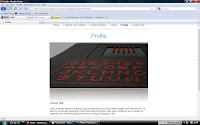
The My Profile Page
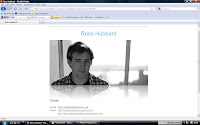
The Contact Me Page
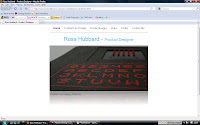
The Home Page
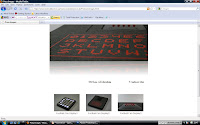
The Press Images Page
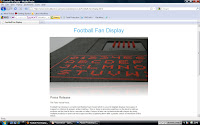
The Press Release Page
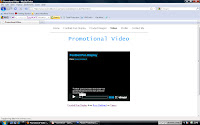
The Video Page
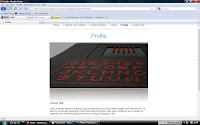
The My Profile Page
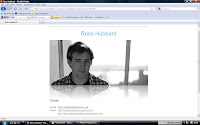
The Contact Me Page
Press Release
This is the press release that i have written to accompany the press images that i have taken to send out to the public domain. It covers what the product is, why it exists and where i can be found exhibiting my work.
Ross Hubbard.
Product Designer.
Football Fan Display
The Fans Visual Voice
Football Fan Display is a hand-held flexible foam board which is used to digitally display messages of support or criticism to players at live matches. This is done by pressing switches on the back to light up sections on the front to form a number or letter. Groups of fans can communicate with players by using multiple products to spell out messages and thus supplying them with a greater sense of interaction at the venue.
Ross Hubbard says “I was inspired by how emotionally invested fans can get especially fans who travel as a group on a regular basis also including season ticket holders. I feel their opinions speak greater volumes than others and they should have a means to express their opinions to players and managerial staff.”
Coming as a variation on the banners that fans bring to matches to show their support and opinions to all attending at the live match. The aim is to allow fans to keep their voice up-to-date through the fast paced nature of the game. The idea behind this item is for this to be a rental item obtainable from merchandise shops before the match and returned afterwards.
The Football Fan Display combines a electronics with foam, The Zotefoam exterior is made using a CNC milling machine, once these parts have been made the character display graphic on the back is applied using screen printing. Plastic parts are vacuum formed, the front ones are then finished by sand blasting, the back plastic parts are laser cut to produce a more accurate finish.
Ross will be exhibiting his Football Fan Display at the Duncan of Jordanstone School of Art and Design degree show from 22/05/2010 to 30/05/2010 with in the School of Product Design.
He will also be exhibiting at New Designers, at the Business Design Centre in London between 08/07/2010 and 11/07/2010.
Retail Price:- TBC
Rental Price:- TBC
-Ends-
Notes to editor:
Ross Hubbard believes in giving a great experience by using simple designs and interactions. He likes to encourage emotional connections which therefore add value.
Product Design at Dundee is a highly successful new course, with students working on a variety of briefs for, Microsoft, Fortnum and Mason, HP and NCR. The course encourages unique designs to be taken from sketchbook to reality.
Press enquires:
Ross Hubbard
Website:- www.rosshubbard.co.uk
E-mail. - Ross.Hubbard@hotmail.co.uk
Ross Hubbard.
Product Designer.
Football Fan Display
The Fans Visual Voice
Football Fan Display is a hand-held flexible foam board which is used to digitally display messages of support or criticism to players at live matches. This is done by pressing switches on the back to light up sections on the front to form a number or letter. Groups of fans can communicate with players by using multiple products to spell out messages and thus supplying them with a greater sense of interaction at the venue.
Ross Hubbard says “I was inspired by how emotionally invested fans can get especially fans who travel as a group on a regular basis also including season ticket holders. I feel their opinions speak greater volumes than others and they should have a means to express their opinions to players and managerial staff.”
Coming as a variation on the banners that fans bring to matches to show their support and opinions to all attending at the live match. The aim is to allow fans to keep their voice up-to-date through the fast paced nature of the game. The idea behind this item is for this to be a rental item obtainable from merchandise shops before the match and returned afterwards.
The Football Fan Display combines a electronics with foam, The Zotefoam exterior is made using a CNC milling machine, once these parts have been made the character display graphic on the back is applied using screen printing. Plastic parts are vacuum formed, the front ones are then finished by sand blasting, the back plastic parts are laser cut to produce a more accurate finish.
Ross will be exhibiting his Football Fan Display at the Duncan of Jordanstone School of Art and Design degree show from 22/05/2010 to 30/05/2010 with in the School of Product Design.
He will also be exhibiting at New Designers, at the Business Design Centre in London between 08/07/2010 and 11/07/2010.
Retail Price:- TBC
Rental Price:- TBC
-Ends-
Notes to editor:
Ross Hubbard believes in giving a great experience by using simple designs and interactions. He likes to encourage emotional connections which therefore add value.
Product Design at Dundee is a highly successful new course, with students working on a variety of briefs for, Microsoft, Fortnum and Mason, HP and NCR. The course encourages unique designs to be taken from sketchbook to reality.
Press enquires:
Ross Hubbard
Website:- www.rosshubbard.co.uk
E-mail. - Ross.Hubbard@hotmail.co.uk
Lulu book Foreword
I have been contacting various people from the world of sports, from Fanzines, Psychologists and Clubs and i had very little response and was pleasantly surprised to receive a reply from a Dr Robert Weinberg. He is a sports psychologist from America and now works for a sports company. I asked if it was possible for him to write a piece to go at the start of my lulu book to provide some context.
His Foreword was as follows:-
Winning and losing and performing well and poorly are all part of sport competition. Many factors go into an athlete’s performance but certainly one of them is the audience. There’s been a lot of research on the home field advantage much emanating from the theoretical perspective of Drive Theory. However, empirical research has sometimes supported the benefit of playing at home whereas other research has demonstrated that playing at home might actually be a disadvantage due to the pressure on the home team. Coaches and athletes spend lots of time preparing to play in front of opposing crowds who can get quite unruly. There are lots of factors affecting a team’s play at home or on the road (e.g., travel, playing surface, officials, etc) but most assuredly fans are an important part of the equation. So the more we can learn about the impact of fans on performance, the better off coaches and athletes will be in terms of preparation.
His Foreword was as follows:-
Winning and losing and performing well and poorly are all part of sport competition. Many factors go into an athlete’s performance but certainly one of them is the audience. There’s been a lot of research on the home field advantage much emanating from the theoretical perspective of Drive Theory. However, empirical research has sometimes supported the benefit of playing at home whereas other research has demonstrated that playing at home might actually be a disadvantage due to the pressure on the home team. Coaches and athletes spend lots of time preparing to play in front of opposing crowds who can get quite unruly. There are lots of factors affecting a team’s play at home or on the road (e.g., travel, playing surface, officials, etc) but most assuredly fans are an important part of the equation. So the more we can learn about the impact of fans on performance, the better off coaches and athletes will be in terms of preparation.
Press Images
Screen Printing
This is the end result of getting screen printing put on the back of my model, this screen printing is there to help the user understand what how to form letters and numbers with the buttons. I got the company Tay Print on the outskirts of Dundee to do the screen printing.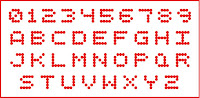
The template that i gave to Tay Print, High Res PDF.
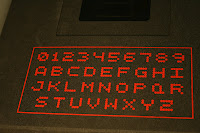
The whole completed foam screen printed.
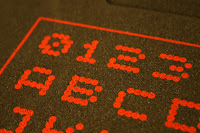
The Close up of the screen printing.
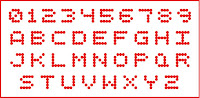
The template that i gave to Tay Print, High Res PDF.
The whole completed foam screen printed.
The Close up of the screen printing.
Sand Blasting
For the front plastic parts i have come to the conclusion that sand blasting provides a better light for the front sections as it lights up the whole area and provides a greater contrast against the foam. This is an image of how it looks with out light, lit section pictures will follow.
It is an easy machine to use with simple instructions, Fong the Sculpture technician give me a quick induction. First turn switch at the isolator, then power box, turn the valve for the air flow. Then open the door and place your piece in the sand blaster and fasten the door closed. You then place your hands in the gloves and take a hold of your work piece and apply the sand by putting pressure on the foot pedal.
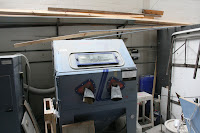
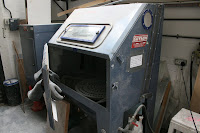
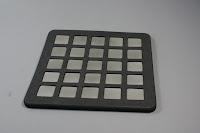
Finished result mounted in the foam.
It is an easy machine to use with simple instructions, Fong the Sculpture technician give me a quick induction. First turn switch at the isolator, then power box, turn the valve for the air flow. Then open the door and place your piece in the sand blaster and fasten the door closed. You then place your hands in the gloves and take a hold of your work piece and apply the sand by putting pressure on the foot pedal.
Finished result mounted in the foam.
Final Foam
After numerous e-mails to and fro i managed to get my final foam, it is being produced by MSA Foams Ltd who are based down in England. The peice was a one of peice and hence cost over 200 pounds to produce and deliver. It is made from LD45 Plastazote foam by Zotek (who were brought to my attention by Pete my tutor. I am very happy with the results it is still relatively rigid considering it is foam. They also sent me some sample pieces so that i could practice attachment and screen printing.
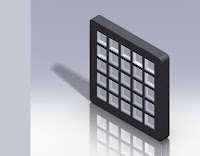
This is the solidworks render that i made to get an idea of how the product would look.
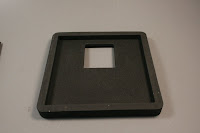
This is one of the final parts that i have got back.
This is the solidworks render that i made to get an idea of how the product would look.
This is one of the final parts that i have got back.
Soldering
This is just an image of me soldering and what the soldering i am working on looks like, i leave alot of spare wire to allow for mistakes that i make. I do have to admit i find soldering quite relaxing. It just a process of twisting wires together or putting the wire through the hole and heating these metal elements and tougching the solder to the iron/metal points to be joined.
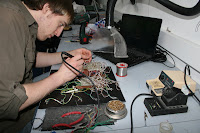
Vacuum Forming
So for the front screen sections i have decided to use transparent 1mm HIPS plastic as it can vacuum form well and be finished afterwards in a number of ways, the back plastic will me made from 1mm black HIPs. These are some pictures i have taken while vacuum forming lately.
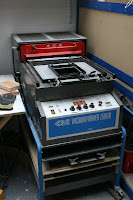
This is the vacuum forming machine, Sean admits that it is not maintained that well considering the use it get, with the vacuum seals only getting replaced every 3 years
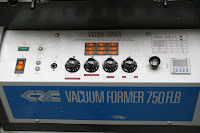
The buttons and dials, all fairly staright forward to use.
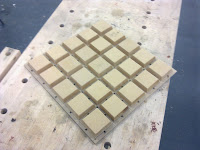
The ambitious first mould of the front plastic, needless to say this did not work but it was then cut into strips and given an extended time under heat the plastic took to the mould well.
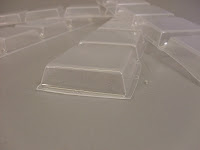
The resultant pieces of clear plastic for the front.
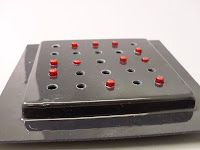
A laser cut, vacuum formed piece for the back of the model.
This is the vacuum forming machine, Sean admits that it is not maintained that well considering the use it get, with the vacuum seals only getting replaced every 3 years
The buttons and dials, all fairly staright forward to use.
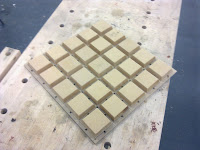
The ambitious first mould of the front plastic, needless to say this did not work but it was then cut into strips and given an extended time under heat the plastic took to the mould well.
The resultant pieces of clear plastic for the front.
A laser cut, vacuum formed piece for the back of the model.
LED's
These are the final LED's i have settled on.
These are from www.superbrightleds.com. These are 360 degree viewing angle, diffused, 8mm white LED's. These illuminate a corner of a dark room running from 3 volts.
These are very bright and. These are very bright and the only down side is that they are expensive to be delivered as they are from the USA.
These are from www.superbrightleds.com. These are 360 degree viewing angle, diffused, 8mm white LED's. These illuminate a corner of a dark room running from 3 volts.
5 x 5 Form
These are some images of the 5 x 5 section form that i have recieved back from engineering, Dave King had taken a holiday and one of the peices came loose from the bae so it was ruined, so it arrived to me about a week late. Sooner rather than later i suppose. I imediately feel more comfortable using this form when talking about my product as it will give greater chracter legability as opposed to the 3x5 grid prototype.
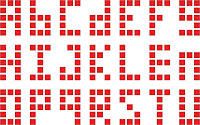
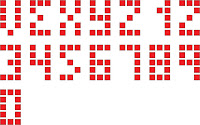
This is the example font that i made up and decided that the 5 x 5 grid was the best way to go.
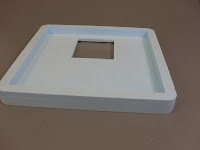

The Blue foam that was made by Dave King on the Mori Sekhi machine.
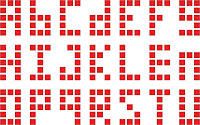
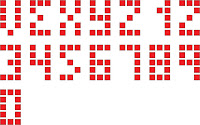
This is the example font that i made up and decided that the 5 x 5 grid was the best way to go.
The Blue foam that was made by Dave King on the Mori Sekhi machine.
Monday 10 May 2010
Drilling PCB
Hand Drilling
- Collect a Hand Drill and Twist Drill Bits. (Pictured)
- Decide how large a hole you need to fit wires through.
- Attach a drill bit and place at the centre of the soldering panel at 90 degrees to the copperboard.
- Apply pressure at end and rotate the shaft section.
- Don’t go to fast or drill at an angle otherwise the drill bit may snap or bend.
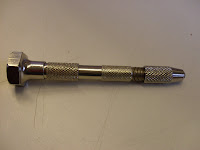
- The Hand Drill
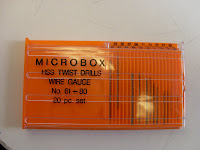
- The Drill Bits
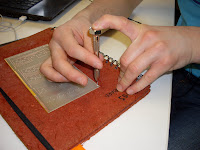
- Me Drilling.
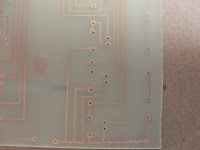
The end results
- Collect a Hand Drill and Twist Drill Bits. (Pictured)
- Decide how large a hole you need to fit wires through.
- Attach a drill bit and place at the centre of the soldering panel at 90 degrees to the copperboard.
- Apply pressure at end and rotate the shaft section.
- Don’t go to fast or drill at an angle otherwise the drill bit may snap or bend.
- The Hand Drill
- The Drill Bits
- Me Drilling.
The end results
Acid Bathing
Acid Bathing
- Obtain the following - Basin, Small Tub, Ferric Chloride Solution, Sponge and Rubber Gloves.
- Fill basin with warm/hot water.
- Fill small tub with acid solution and submerge copperboard in acid.
- Place small tub within basin, (Leave for 1hour).
- Remove copperboard, wipe well with acid soaked sponge, return to solution. (Leave for 15mins).
- Repeat until all uncovered copper has been worn away.
- Return solution to initial container, clean all items used thoroughly and rinse and scrub sink well.
!!WEAR GLOVES AT ALL TIMES!!
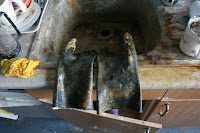
- Gloves
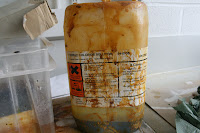
- Ferric Chloride Solution
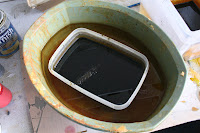
- The copperboard bathing in the acid solution.
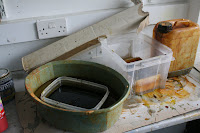
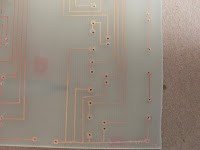
-The end result.
- Obtain the following - Basin, Small Tub, Ferric Chloride Solution, Sponge and Rubber Gloves.
- Fill basin with warm/hot water.
- Fill small tub with acid solution and submerge copperboard in acid.
- Place small tub within basin, (Leave for 1hour).
- Remove copperboard, wipe well with acid soaked sponge, return to solution. (Leave for 15mins).
- Repeat until all uncovered copper has been worn away.
- Return solution to initial container, clean all items used thoroughly and rinse and scrub sink well.
!!WEAR GLOVES AT ALL TIMES!!
- Gloves
- Ferric Chloride Solution
- The copperboard bathing in the acid solution.
-The end result.
Sunday 11 April 2010
Copperboard and Lazer Cutter
So the next stage of making a PCB is acquiring the Copper Board. Martin and i bought at the same time, ordering through Rapid electronics through the college art shop, therefore saving some money. The Copper board is called Plain Copper clad board, code from the Rapid 09 catalog is (34-0810). This took a few days to arrive, once it arrives you have to spray it evenly with a spray paint.
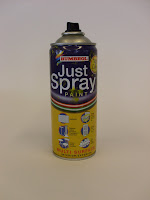
The Spray paint ( yellow works best )
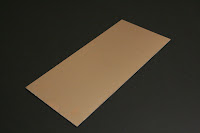
The Plain Copper Clad Board
So when you bring the mirrored PDF file from Fritzing and put it into the lazer cutter you are aiming to remove the paint from the areas where you do not want copper on the PCB. So therefore leaving the paint over the copper you want to keep. I would highly recommend you do a test piece on card to ensure that it is working correctly.
For settings i used 50 power and 50 speed, but it varies heavily with others using 70/70 and 90/40. So it may take a second pass. Be sure that it is all the way through the paint to make sure the Acid bathing works properly.
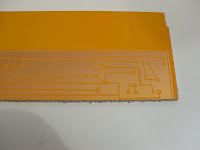
This one needs to go in the laser cutter again as the copper does not show through properly.
The Spray paint ( yellow works best )
The Plain Copper Clad Board
So when you bring the mirrored PDF file from Fritzing and put it into the lazer cutter you are aiming to remove the paint from the areas where you do not want copper on the PCB. So therefore leaving the paint over the copper you want to keep. I would highly recommend you do a test piece on card to ensure that it is working correctly.
For settings i used 50 power and 50 speed, but it varies heavily with others using 70/70 and 90/40. So it may take a second pass. Be sure that it is all the way through the paint to make sure the Acid bathing works properly.
This one needs to go in the laser cutter again as the copper does not show through properly.
Friday 9 April 2010
Fritzing
After expressing an interest in making a chipboard I was told that I should download the Fritzing program from this site (http://fritzing.org/). This is the software is free and is very similar to the program used in engineering called EasyPCB, i decided not to go to engineering as it could have cost money and i also wanted a program that i could work on in the studio and at ho
me.
Placing the parts in Fritzing.
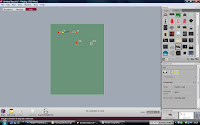
Attaching the parts in Fritzing.
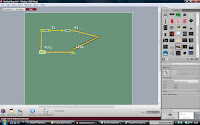
Making extra connecting nodes.
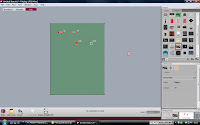
Placing the parts in Fritzing.
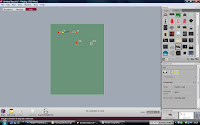
Attaching the parts in Fritzing.
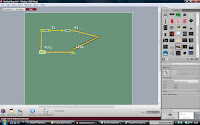
Making extra connecting nodes.
Subscribe to:
Posts (Atom)